Lyfecycle is the world’s first fully recyclable* and biodegradable plastic technology
*When products are collected for recycling
Recyclable
Time-set biodegradation
Microplastic free
Toxin free
Our next-gen sustainable products
Toilet paper bag
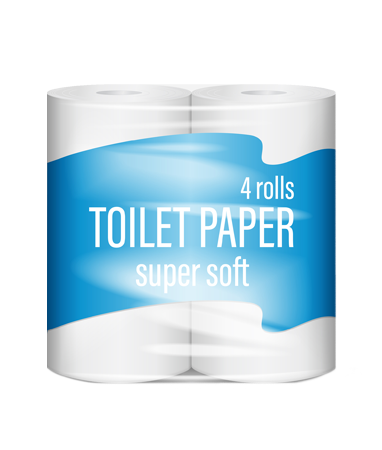
Flower sleeves
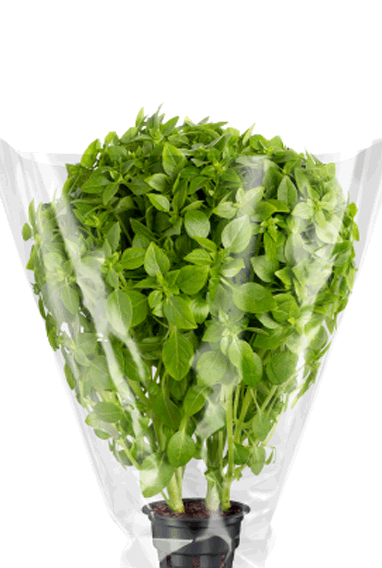
Produce bags

Confectionary wrappers & labels
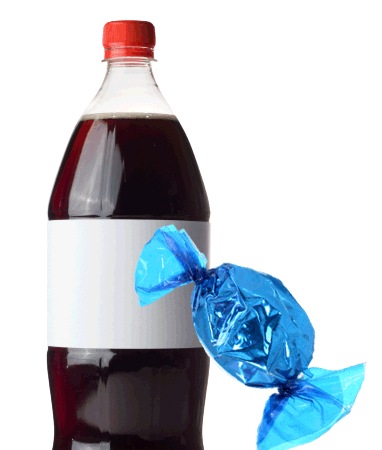
Bread Bags
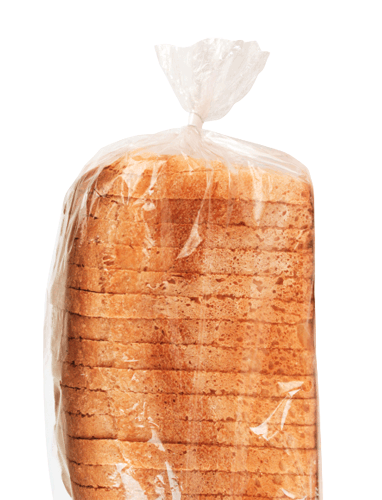
Detergent bottle
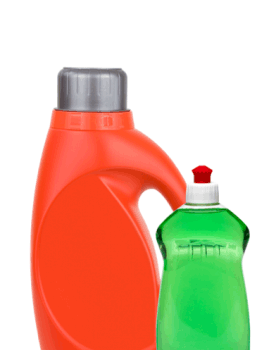
Drinking straws
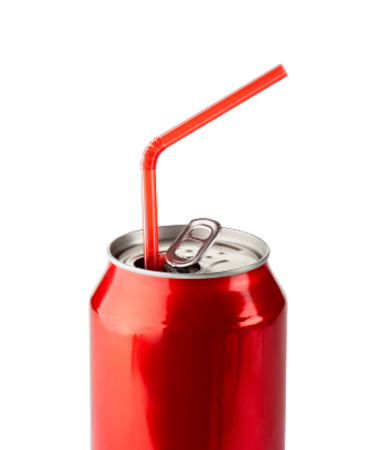
Thin wall containers
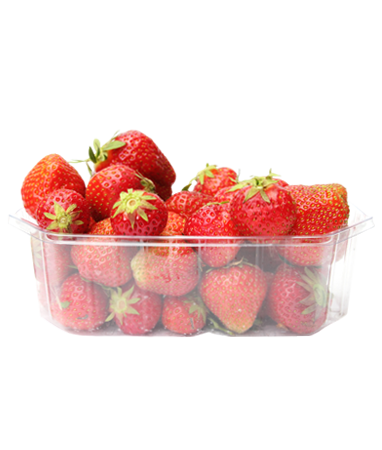
Drinking cups
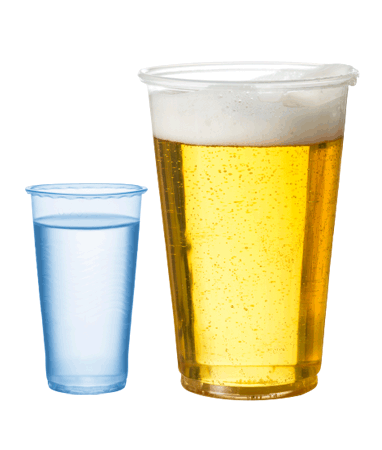
Garment Polybags
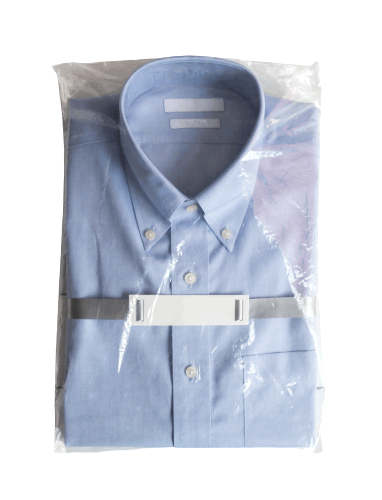
Stretch film
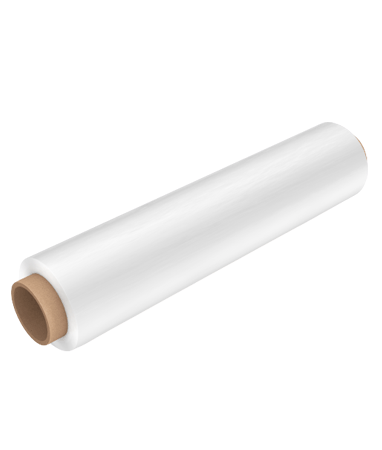
Shrink wrap
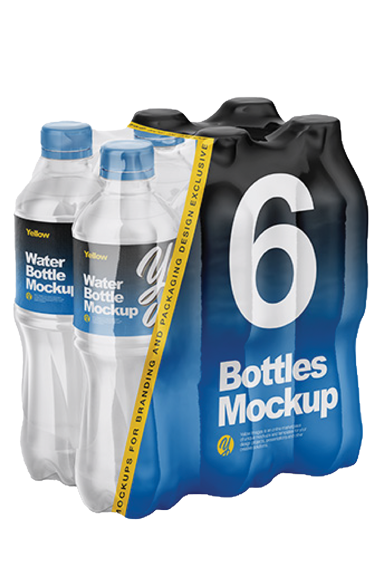
NEXT-GEN SUSTAINABLE
Toilet paper bag
Toilet paper bag (but not limited to)
P/F Criteria | – 50 micron | – 50 micron, matte finish | |
---|---|---|---|
Thickness | Microns | 50 | 50 |
Manufacturing process | Blown Film Extrusion | Blown Film Extrusion | |
Pigments/Additives | None | None | |
CI | >1 | 1.59 | 1.18 |
Reduction in Mw (%) | >90% | 97.8% | 96.2% |
Mn (Da) | <5,000 Da | 533 Da | 1,067 Da |
Mz (Da) |
Graph showing the % biodegradation of the samples over time
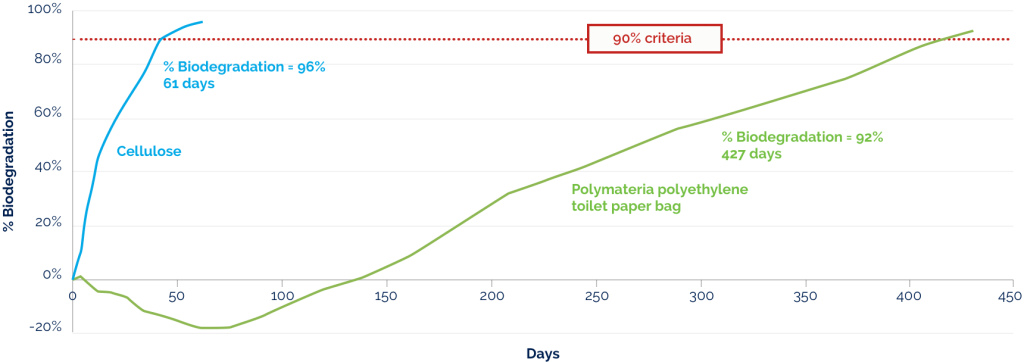
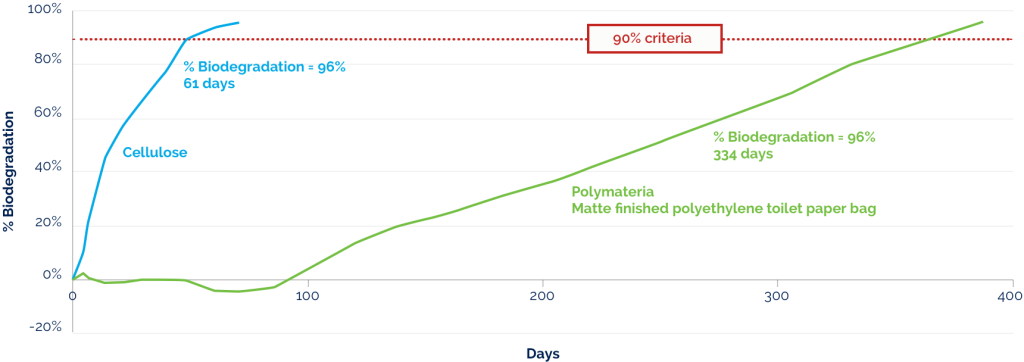
The results show the % biodegradation of toilet paper bags containing Polymateria’s technology weathered to the strict Pass/Fail criteria specified in PAS 9017:2020. To mimic the natural environment, the biodegradation of the resulting wax was carried out in natural soil.
Naturally occurring microbes such as bacteria and fungi recognised the wax as a food source and converted the wax to carbon dioxide through a process known as respiration. The % biodegradation was calculated by determining the conversion of the total organic carbon in the wax into carbon dioxide. While standard laboratory methods allow a two-year long testing period, the resulting wax from Polymateria’s technology achieved greater than 90 % biodegradation in less than a year.
NEXT-GEN SUSTAINABLE
Flower sleeves
Flower Sleeves includes (but not limited to)
P/F Criteria | Flower Sleeve | |
---|---|---|
Thickness | Microns | 25 |
Manufacturing process | Extrusion + Biorentation | |
Pigments/Additives | None | |
CI | >1 | 1.22 |
Reduction in Mw (%) | >90% | 97.4% |
Mn (Da) | <5,000 Da | 1,850 Da |
Mz (Da) | <30,000 Da | 26,789 Da |
Produce bags
Range of Produce Bags includes (but not limited to)
P/F Criteria | Polyethylene Bag | |
---|---|---|
Thickness | Microns | 14 |
Manufacturing process | Blown Film Extrusion | |
Pigments/Additives | 4% CaCO3 | |
CI | >1 | 1.59 |
Reduction in Mw (%) | >90% | 97.5% |
Mn (Da) | <5,000 Da | 667 Da |
Mz (Da) | <30,000 Da | 8,000 Da |
NEXT-GEN SUSTAINABLE
Confectionary wrappers & labels
Range of Wrappers and Labels (but not limited to)
P/F Criteria | Three-layer BOPP | Five-layer BOPP | |
---|---|---|---|
Thickness | Microns | 25 | 25 |
Manufacturing process | Extrusion + Biorentation | Extrusion + Biorentation | |
Pigments/Additives | None | None | |
CI | >1 | 1.19 | 1.22 |
Reduction in Mw (%) | >90% | 97.6% | 97.4% |
Mn (Da) | <5,000 Da | 3,850 Da | 1,850 Da |
Mz (Da) | <30,000 Da | 15,000 Da | 26,789 Da |
NEXT-GEN SUSTAINABLE
Bread Bags
Range of Bread Bags (but not limited to)
P/F Criteria | 3 Layered Films | Multi-layer PP+PE Films | Multi-layer PE Films | |
---|---|---|---|---|
Thickness | Microns | 50 | 19 | 60 |
Manufacturing process | Blown Film | Blown Film | Blown Film | |
Pigments/Additives | None | None | None | |
CI | >1 | 1.18 | 1.38 | 1.17 |
Reduction in Mw (%) | >90% | 92.5% | 96.9% | 93.2% |
Mn (Da) | <5,000 Da | 1,757 Da | 1,020 Da | 1,400 Da |
Mz (Da) | <30,000 Da | 28,167 Da | 10,667 Da | 28,769 Da |
NEXT-GEN SUSTAINABLE
Detergent bottle
Detergent Bottle (but not limited to)
P/F Criteria | Detergent Bottle | |
---|---|---|
Thickness | Microns | 800 |
Manufacturing process | Injection Moulding | |
Pigments/Additives | None | |
CI | >1 | 2.12 |
Reduction in Mw (%) | >90% | 98.8% |
Mn (Da) | <5,000 Da | 1,867 Da |
Mz (Da) | <30,000 Da | 11,200 Da |
Graph showing the % biodegradation of the samples over time
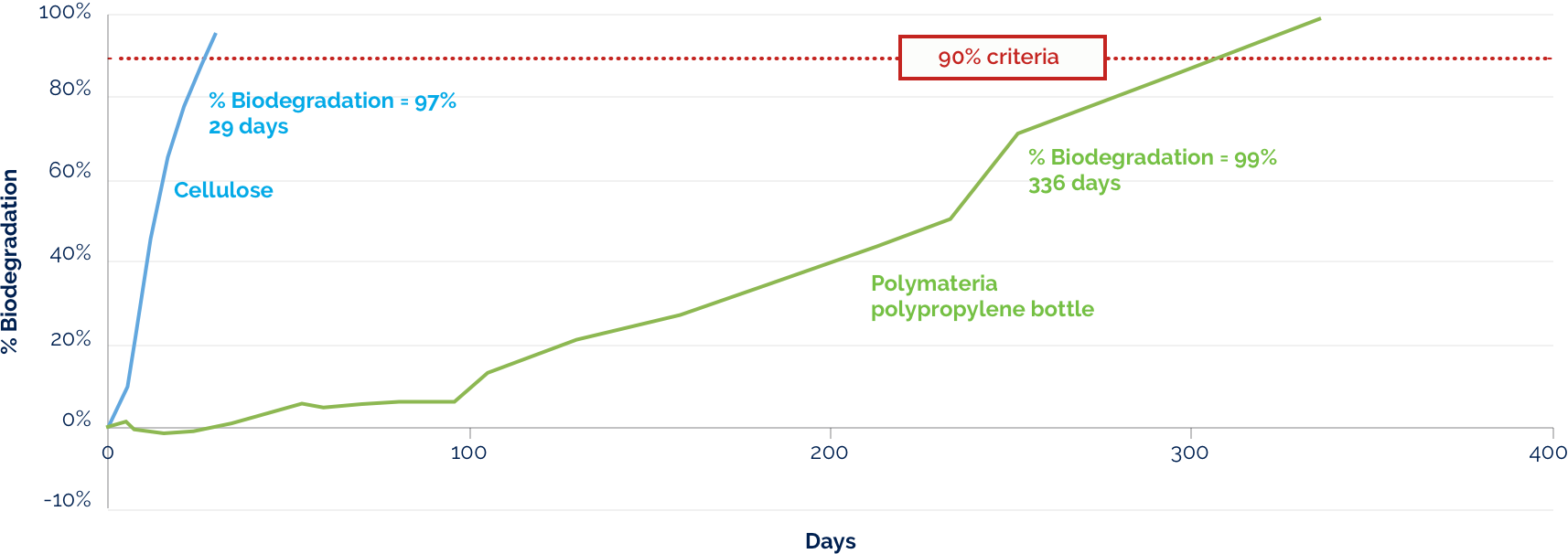
The results show the % biodegradation of a detergent bottle containing Polymateria’s technology weathered to the strict Pass/Fail criteria specified in PAS 9017:2020. To mimic the natural environment, the biodegradation of the resulting wax was carried out in natural soil.
Naturally occurring microbes such as bacteria and fungi recognised the wax as a food source and converted the wax to carbon dioxide through a process known as respiration. The % biodegradation was calculated by determining the conversion of the total organic carbon in the wax into carbon dioxide. While standard laboratory methods allow a two-year long testing period, the resulting wax from Polymateria’s technology achieved greater than 90 % biodegradation in less than a year.
NEXT-GEN SUSTAINABLE
Drinking straws
Range of Drinking Straws includes (but not limited to)
P/F Criteria | Straw | Straw Sleeve | |
---|---|---|---|
Thickness | Microns | 160 | 19 |
Manufacturing process | Die Extrusion | Blown Film | |
Pigments/Additives | None | None | |
CI | >1 | 1.23 | 1.38 |
Reduction in Mw (%) | >90% | 97.9% | 96.9% |
Mn (Da) | <5,000 Da | 1,710 Da | 1,020 Da |
Mz (Da) | <30,000 Da | 19,667 Da | 10,667 Da |
Thin wall containers
Range of Thin Wall PP Containers includes (but not limited to)
P/F Criteria | PP Container | PP Dessert Pot | PP Noodle Pot | PP Ice Cream Tub | |
---|---|---|---|---|---|
Thickness | Microns | 700 | 300-400 | 650 | 500 |
Manufacturing process | Thermoforming | Injection Moulding | Injection Moulding | Injection Moulding | |
Pigments/Additives | Black (2-3%) | Yellow (0.2%) | Yellow (2%) | Silver (2%) | |
CI | >1 | 1.60 | 1.37 | 1.60 | 1.62 |
Reduction in Mw (%) | >90% | 98.6% | 97.8% | 96.3% | 97.8% |
Mn (Da) | <5,000 Da | 1,967 Da | 1,433 Da | 2,709 Da | 1,667 Da |
Mz (Da) | <30,000 Da | 16,200 Da | 16,333 Da | 9,675 Da | 11,000 Da |
NEXT-GEN SUSTAINABLE
Drinking cups
Range of cups includes (but not limited to)
P/F Criteria | 0.2-0.3L Cup | 0.5L Cup | 0.5L Cup | |
---|---|---|---|---|
Thickness | Microns | 200 | 300 | 500 |
Manufacturing process | Thermoformed | Thermoformed | Injection Moulding | |
Pigments/Additives | None | None | None | |
CI | >1 | 1.27 | 1.38 | 1.09 |
Reduction in Mw (%) | >90% | 97.7% | 98.2% | 96.9% |
Mn (Da) | <5,000 Da | 2,267 Da | 2,267 Da | 3,833 Da |
Mz (Da) | <30,000 Da | 14,667 Da | 9,499 Da | 19,667 Da |
NEXT-GEN SUSTAINABLE
Garment Polybags
Range on Garment/Polybags (but not limited to)
P/F Criteria | Thick Polyethylene Garment Bag | Thin Polyethylene Garment Bag | Clothing Label Tag | |
---|---|---|---|---|
Thickness | Microns | 100 | 75 | 30 |
Manufacturing process | Blown Film Extrusion | Blown Film Extrusion | Injection Moulding | |
Pigments/Additives | None | None | None | |
CI | >1 | 1.53 | 1.71 | 2.10 |
Reduction in Mw (%) | >90% | 96.2% | 97.1% | 98.6% |
Mn (Da) | <5,000 Da | 1,017 Da | 760 Da | 1,149 Da |
Mz (Da) | <30,000 Da | 9,667 Da | 6,800 Da | 6,361 Da |
NEXT-GEN SUSTAINABLE
Stretch film
Stretch Film includes (but not limited to)
P/F Criteria | Stretch Film | |
---|---|---|
Thickness | Microns | 20 |
Manufacturing process | Cast Film Extrusion | |
Pigments/Additives | A Green MB and a Processing aid | |
CI | >1 | 1.38 |
Reduction in Mw (%) | >90% | 96.3% |
Mn (Da) | <5,000 Da | 900 Da |
Mz (Da) | <30,000 Da | 8,667 Da |
NEXT-GEN SUSTAINABLE
Shrink wrap
P/F Criteria | Mono-layer Shrink | Multi-layer Shrink | Multi-layer Shrink Containing 29% HDPE | Multi-layer Shrink Containing 31% HDPE | Bubble Wrap | |
---|---|---|---|---|---|---|
Thickness | Microns | 87.5 | 60 | 70 | 25 | 60 |
Manufacturing process | Blown Film | Blown Film | Blown Film | Blown Film | Extrusion | |
Pigments/Additives | None | None | None | None | None | |
CI | >1 | 1.87 | 1.73 | 1.63 | 1.77 | 2.04 |
Reduction in Mw (%) | >90% | 98.3% | 93.2% | 96.4% | 96.6% | 98.3% |
Mn (Da) | <5,000 Da | 507 Da | 1,400 Da | 1,100 Da | 1,130 Da | 410 Da |
Mz (Da) | <30,000 Da | 19,333 Da | 28,769 Da | 20,000 Da | 16,333 Da | 3,867 Da |
Graph showing the % biodegradation of the samples over time
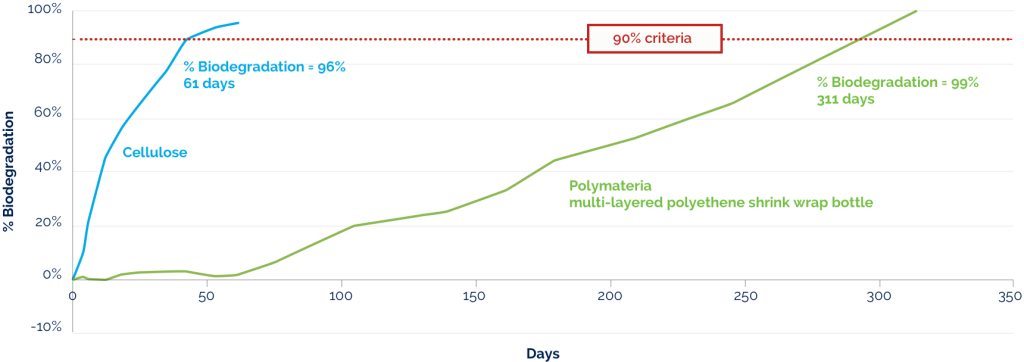
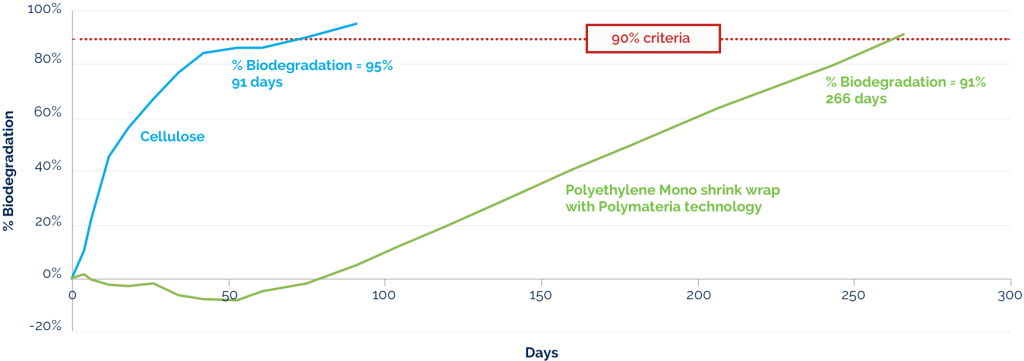
The results show the % biodegradation of a Multi-layered polyethylene shrink wrap containing Polymateria’s technology weathered to the strict Pass/Fail criteria specified in PAS 9017:2020. To mimic the natural environment, the biodegradation of the resulting wax was carried out in natural soil.
Naturally occurring microbes such as bacteria and fungi recognised the wax as a food source and converted the wax to carbon dioxide through a process known as respiration. The % biodegradation was calculated by determining the conversion of the total organic carbon in the wax into carbon dioxide. While standard laboratory methods allow a two-year long testing period, the resulting wax from Polymateria’s technology achieved greater than 90 % biodegradation in less than a year.